1.Determine the characteristics of the materials to be crushed
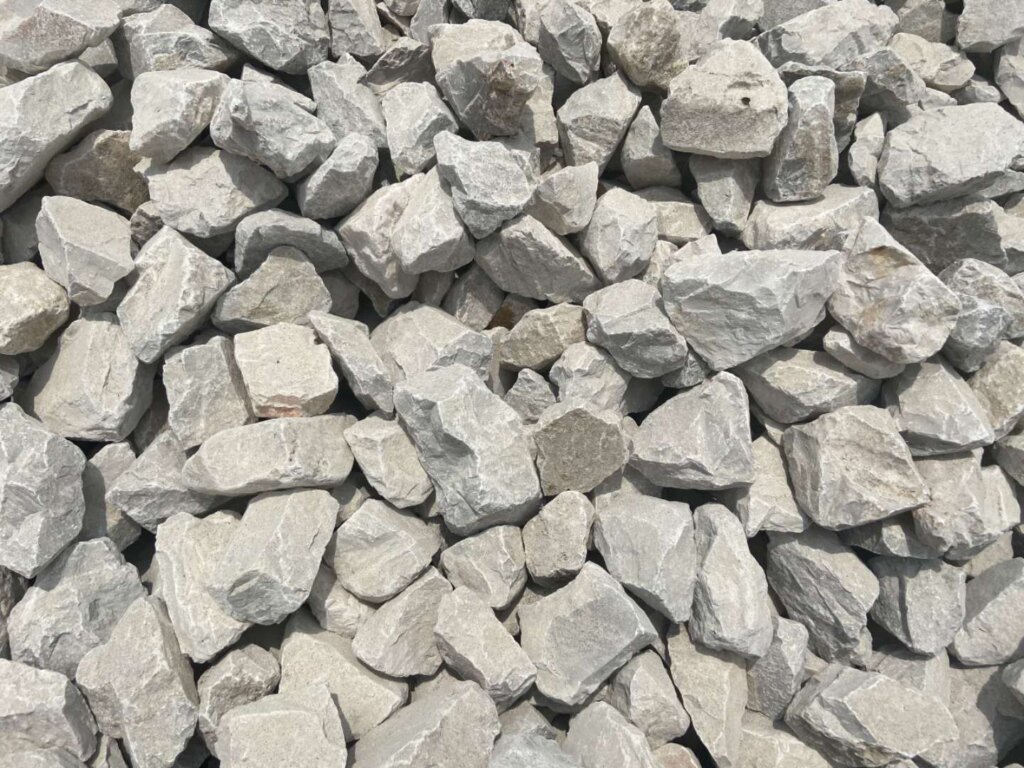
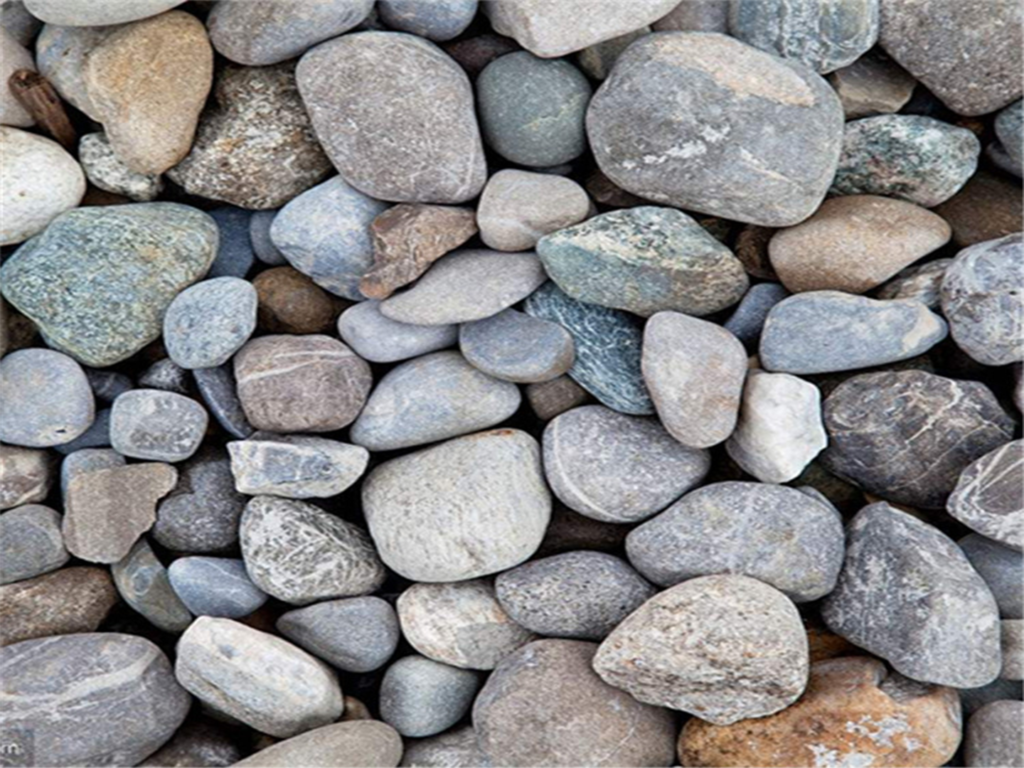
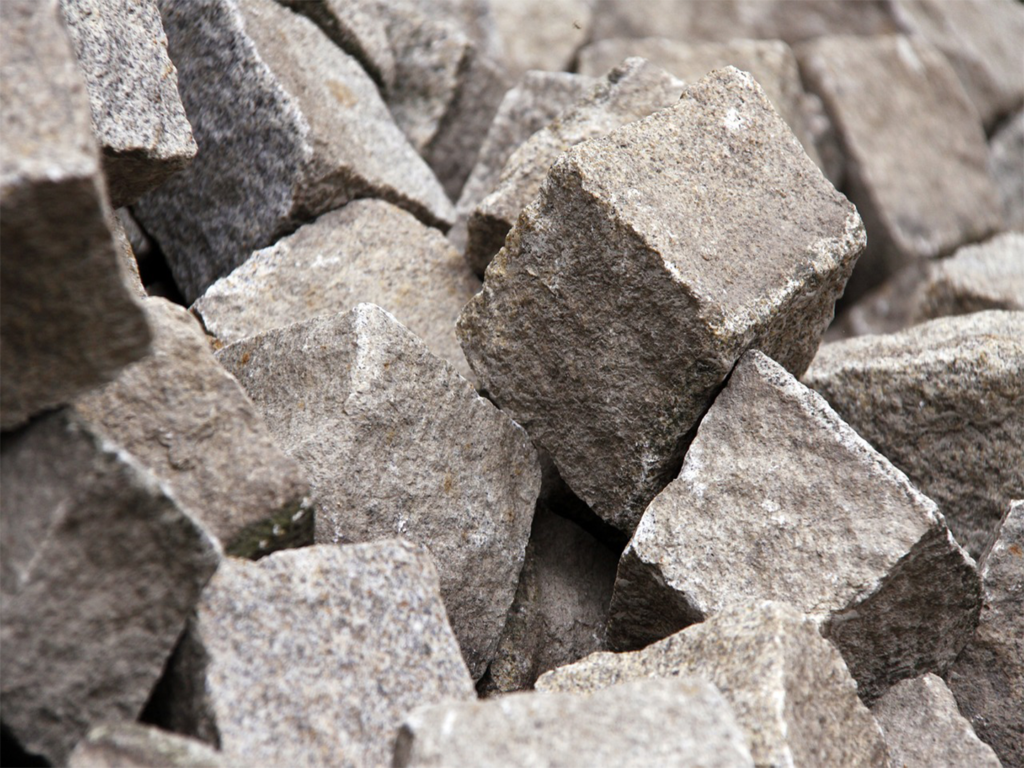
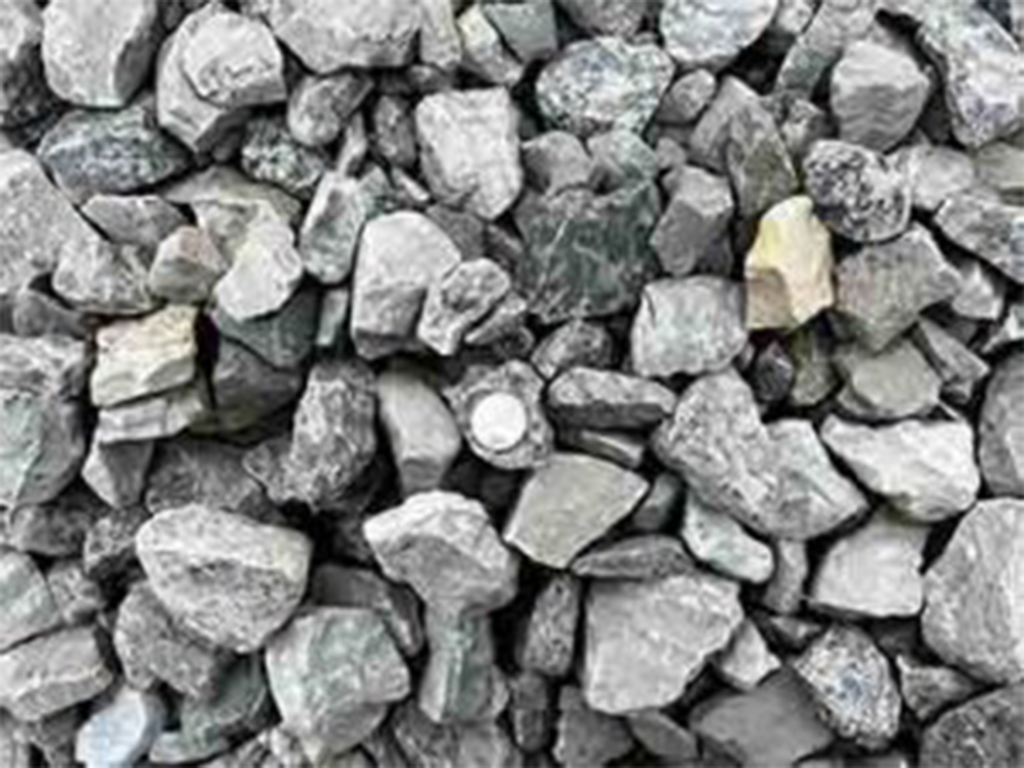
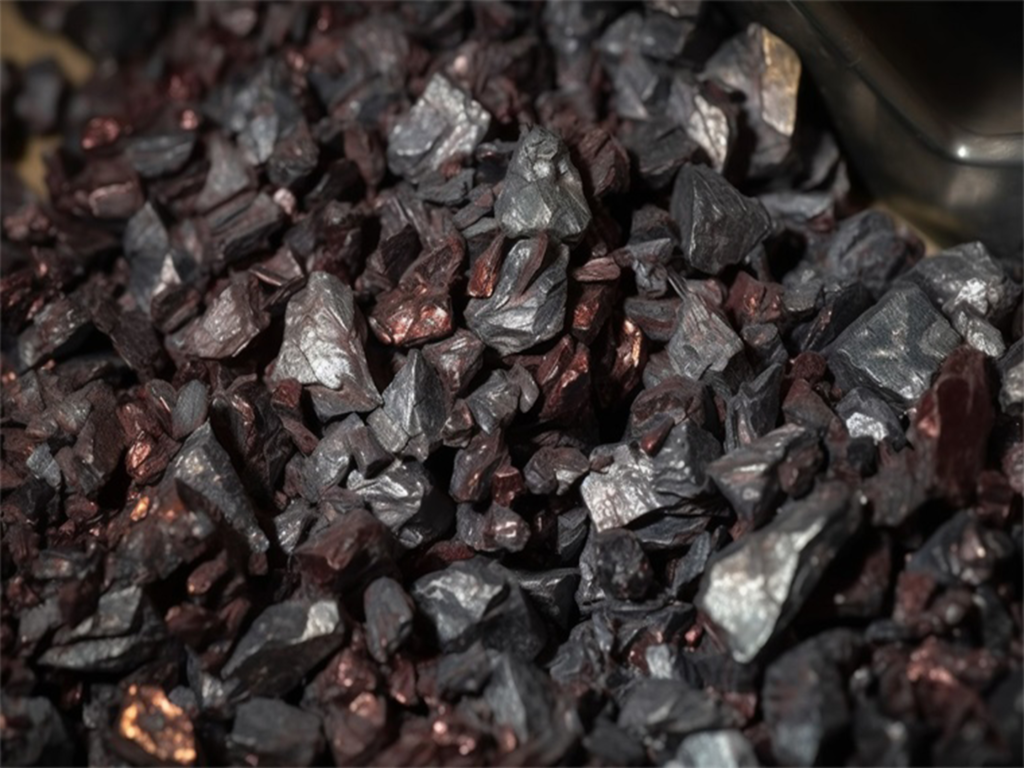
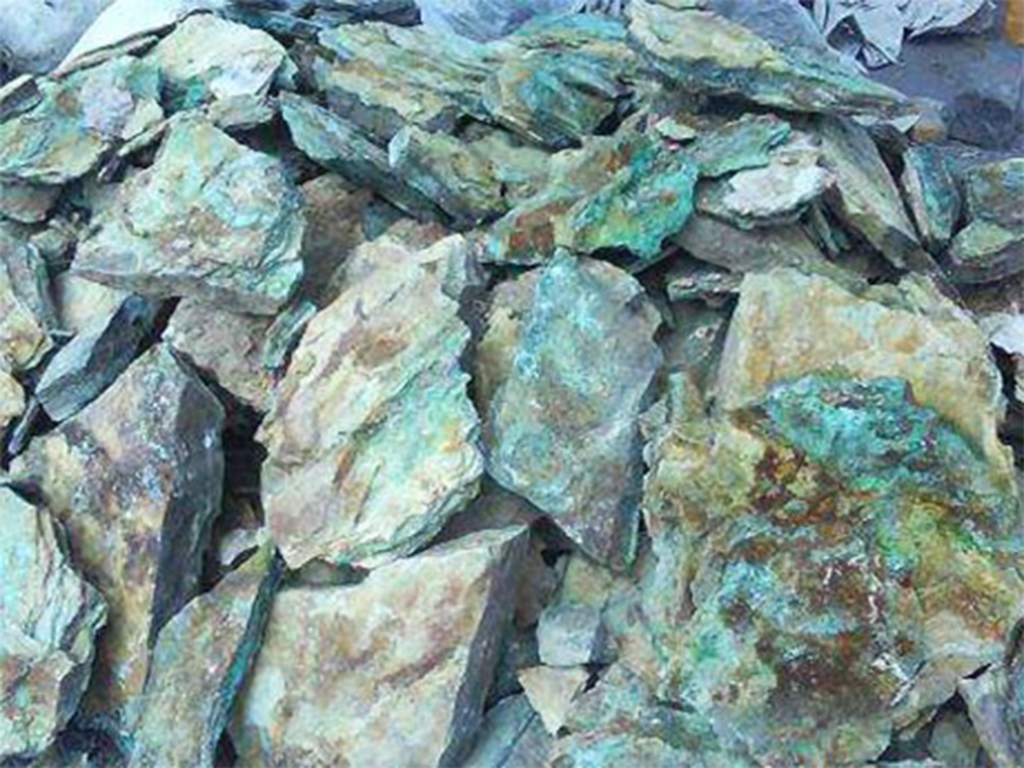
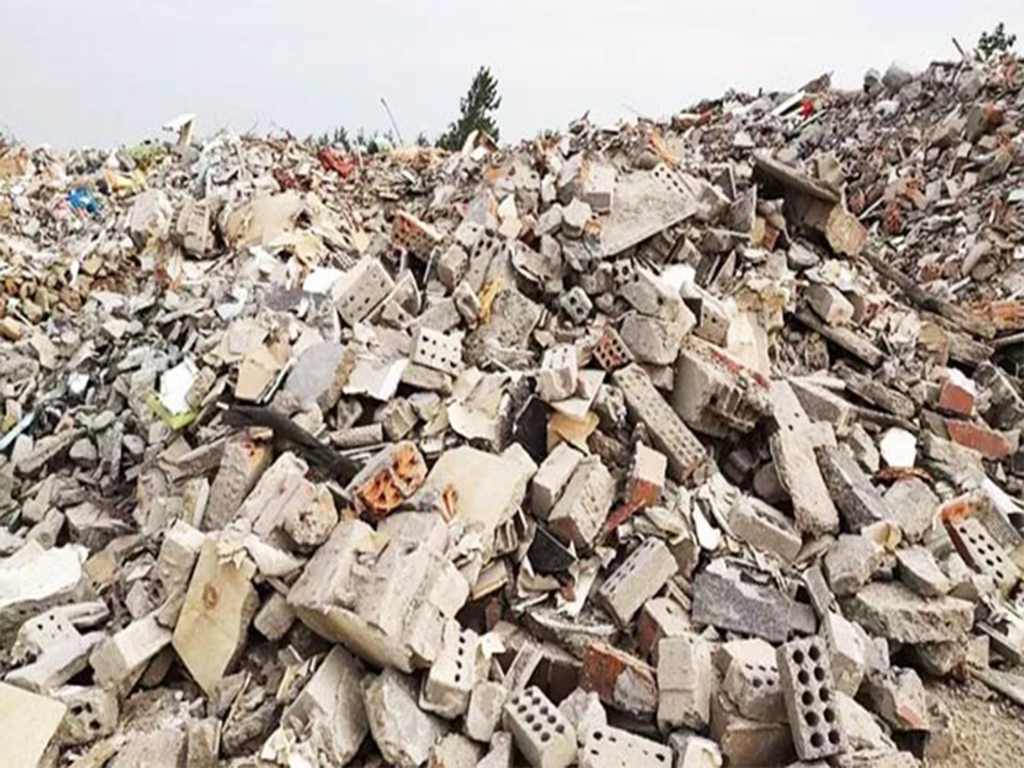
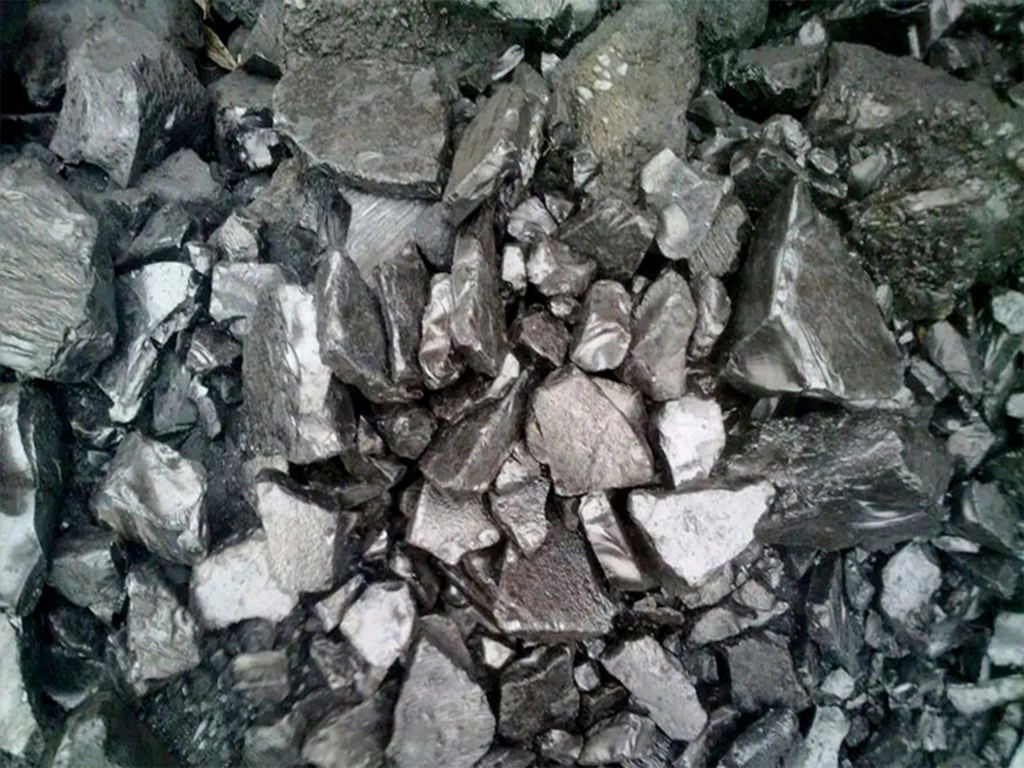
♦Hardness:
For hard materials (such as granite), cone crushers and so on can be selected, while for soft materials (such as limestone), impact crushers can be used.
♦Humidity and stickiness:
For materials with high humidity and strong stickiness, equipment with anti-blocking design should be considered.
♦Particle size:
Appropriate crushing combinations should be selected according to the particle size of the original materials and the requirements for the finished products.
2.Production Capacity and Processing Scale
♦Estimating Production Quantity Requirements
First, define your production goals. For small construction site waste, a few to tens of tons per hour may suffice. For large mine ore crushing, hundreds of tons per hour might be needed. E.g., for a small mine with 1,000 tons of ore daily, a tracked crusher with 50 – 100 tons per hour is suitable.
♦Matching the Project Schedule
Think about the project’s duration and schedule. If time is tight and large amounts need quick processing, pick a high-capacity crusher. Also consider raw material supply stability. For intermittent supply, choose based on peak amount or a flexible-capacity crusher to avoid idleness or overwork.
3. Requirements for mobility and flexibility
♦Mobility Performance
The advantage of the tracked crushing station lies in its good mobility. If the terrain of the working site is complex, such as mountainous mines or rugged construction sites, the tracked crushing station can move easily and adapt to different working locations. It can change positions without good roads and work stably on the ground with a certain slope. For example, in a small quarry in the mountainous area, the tracked crushing station can move along the hillside and carry out crushing operations following the ore mining face.
♦ Adaptability to Site Layout
Consider the flexibility of the crushing station’s layout at the working site. Some tracked crushing stations can be conveniently combined and connected with other equipment, such as feeders, conveyors, screening equipment, etc., to form a complete production line. Moreover, its size and shape should be able to adapt to different site spaces, enabling it to be reasonably arranged even in narrow sites while ensuring good material transfer and work coordination among the equipment.
4.Maintenance and Service Costs
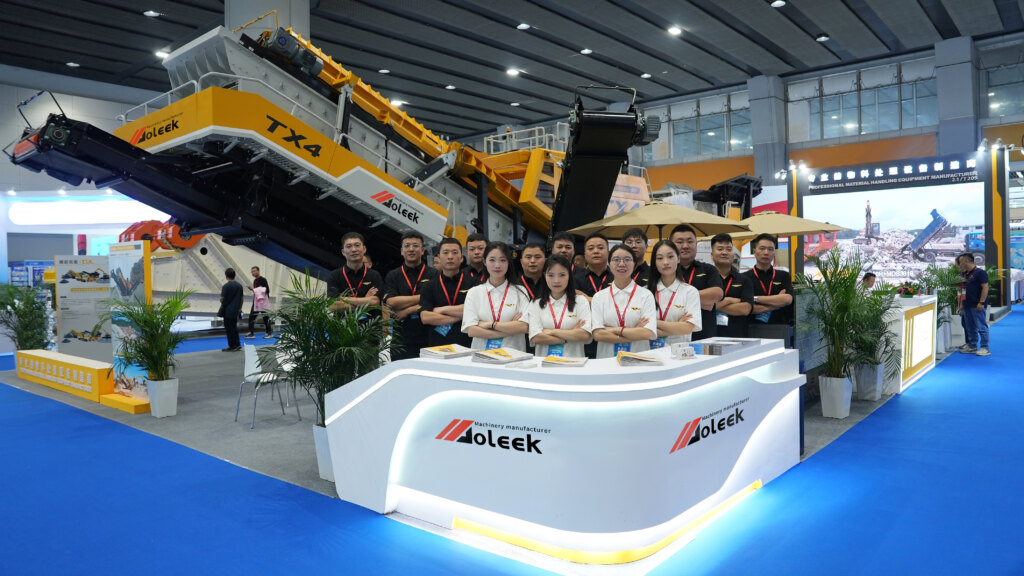
♦Replacement Costs of Wearing Parts
Crushing station’s wearing parts like crusher hammers, liners, conveyor belts. Pick equipment with fairly priced and accessible wear parts. Renowned brand’s tracked crushers often have more suppliers, lower replacement cost. Long service life of wear parts cuts replacement frequency and maintenance cost.
♦Difficulty of Daily Maintenance
Equipment’s daily upkeep should be easy. Its structure conducive to inspection and repair, with enough access and space. Control system should offer fault diagnosis for quick problem spotting. Some tracked crushers use modular design. A faulty module can be replaced fast to reduce downtime.
♦Quality of After-sales Service
Good after-sales ensures timely problem-solving. Opt for suppliers with pro teams and quick response. They should give tech support (remote & on-site) and equipment training for better operation and maintenance.